Demister XL Filtration Systems
The Demister XL Filtration System uses a three-stage process to filter grease, oil and particulate from the exhaust air stream. The Demister XL uses a multi-stage filtration process including velocity reduction, change in direction, water spray scrubbing and demister pad filtration. The air is discharged downward into the larger area of the filter vessel resulting in lower air speeds. The exhaust is also forced to change direction and together with water spray scrubbing action, causes the larger particles to be removed from the exhaust air. The exhaust air then passes through specially designed demister filters to capture as much of the remaining grease and oil as possible. There are no moving components in the demister vessel. The filters are automatically rinsed while in production and the filtered grease, oil or particulate is continuously washed from the vessel by the water flow.
Specifications
1Weather Enclosure
- Encloses the motor and blower assembly to protect from the weather elements, ships assembled with the blower
- Solid floor with angle base, carbon steel construction with air inlet top
- Access doors for electrical maintenance and manual damper adjustment
- Acoustic lining available to reduce noise
2Pressure Blower
- Located on the roof for noise reduction and floor space savings
- The blower will never come in contact with the exhaust stream, so it is more reliable and typically will not have to be cleaned
3Venturi Exhauster
Superior design and precision manufacturing make the Quickdraft Venturi Exhauster the most efficient, consistent and reliable method for maintaining process exhaust requirements.
- No obstructions to the exhaust flow and all moving parts are external to the air stream
- Little or no maintenance
- Consistent, dependable exhaust performance
- Duct can be thoroughly cleaned without harming the blower
- Designed for 24/7 operation
- Long service life
4Exhaust Filtration & Demister Filters
- A three-stage process is used to remove grease, oil and particulate from the exhaust air stream
– Knockdown and Velocity Reduction are used to slow the exhaust air stream and allow larger particles to fall out of the exhaust flow
– Water spray showers located at optimum locations are used to “scrub” the airflow of grease, oil and particulates
– A specially designed series of Demister filter pads capture as much of the remaining grease, oil and particulates as possible. - Filter material is engineered specifically to the maximum temperature of the exhaust flow and the specifics of the application
- Periodic timed spray showers rinse the filters in place during production to maintain system effectiveness
- Filters easily slide out of the Demister XL vessel so that they can be cleaned without fully removing them from the vessel
- Filters are heat-resistant, woven-poly material
5Reduced Footprint
- Save valuable processing floor space with the Demister XL
- The water recirculation unit is housed inside the Demister XL body
6Water Recirculation
- Significantly reduces water consumption in the Demister XL
- Incorporated within the Demister XL vessel to save floor space
- Provides required flow for maximum filtration efficiency
- Includes controls for flow adjustment and timing
7Oven/Fryer/Microwave
Quickdraft works closely with many manufacturers who supply ovens, fryers, blanchers, washers, mixers, etc., for the food industry. Our systems are designed for the manufacturer’s recommended exhaust flow and exhaust temperature for your process.
Features and Benefits
- No moving components, easy to maintain and clean
- 99% efficient for particles 5 micron and greater
- 80% efficient for 3 micron particulate
- All stainless construction
- Water recirculation reduces water consumption and operating costs
- An excellent solution for exhaust from heavy breading applications
Extend the useful life of your roof by keeping it clean
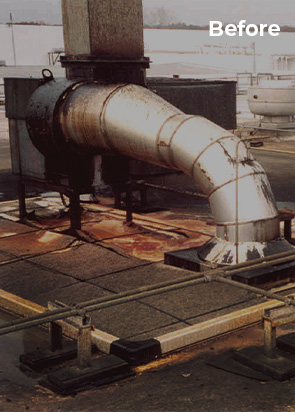
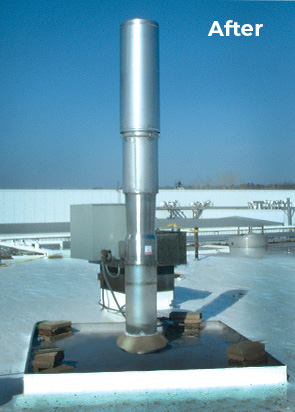
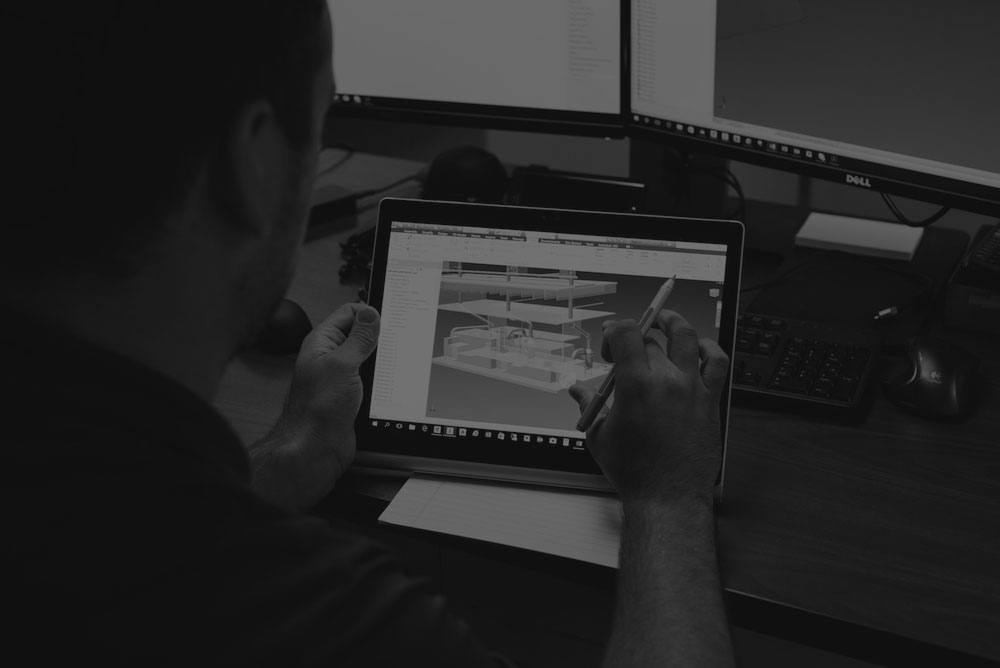
Venturi-Powered Systems
Explore the most efficient method for conveying material without moving parts.
Learn More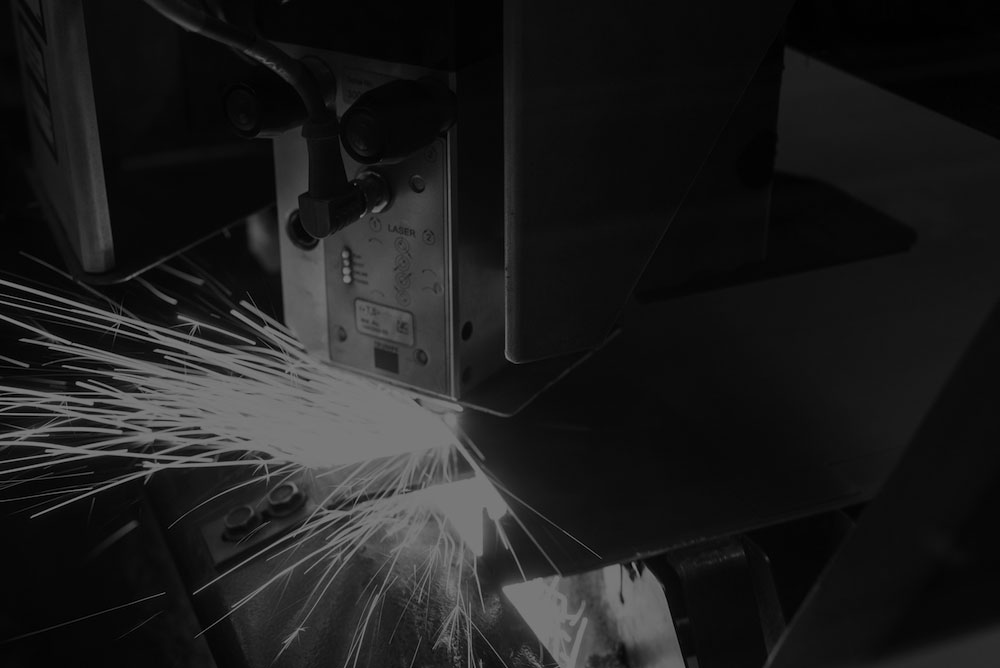
Engineering and Manufacturing
Learn about our engineering design, fabrication, assembly and finishing capabilities.
Learn More